Swiss eBus Plus
This project aims to develop a new generation of electric urban buses to address the main challenges related to electric transport, i.e., the achievable driving range.
We approach the challenge from two directions. First, we focus on the charging infrastructure and develop a reusable software tool to facilitate the planning of electrification of transport systems. Second, we are reducing the energy consumption of on-board thermal systems by proposing intelligent thermal management algorithms to mitigate range problems, especially in cold climates.
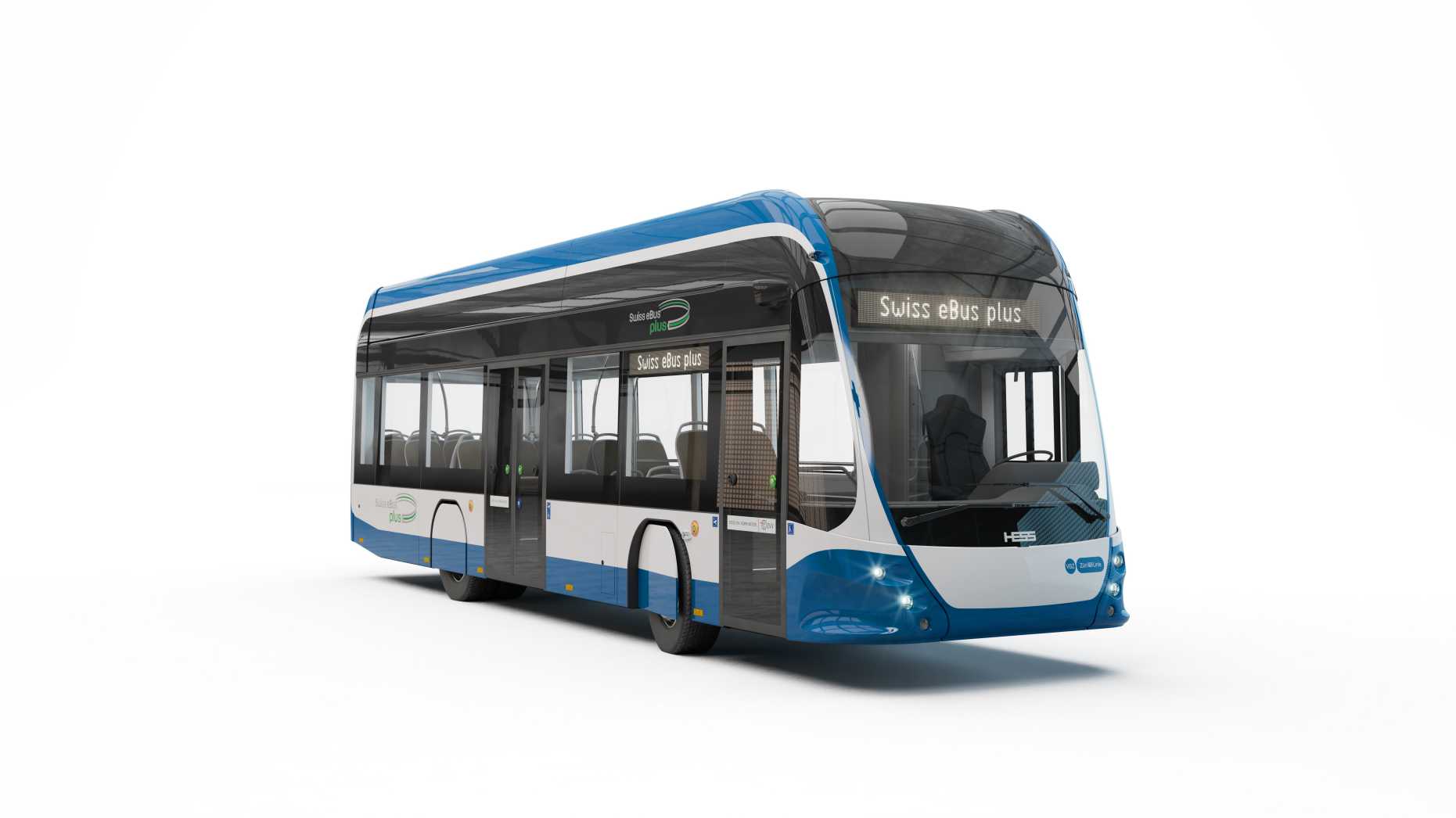
The project Swiss eBus Plus aims to launch a new generation of electric city buses. The advantage of electromobility is obvious: it allows considerable savings in fuel, pollutants and noise, from which passengers, residents and the environment benefit. However, compared to diesel-powered alternatives, electric buses still suffer from disadvantages in terms of necessary infrastructure (charging stations or overhead trolley lines) or achievable driving range (see research field A below). In this project, these challenges are tackled by incorporating the newest technology in core components such as generation 3a battery cells and a CO2 heat pump, both of which allow a lighter build and more efficient operation of the vehicle. In addition, the vehicle structure is optimized for thermal performance, for instance, by employing double-glazed windows, improved insulation, and air curtains. Finally, the operation of the vehicle is to be optimized, mainly in terms of its thermal management (see research field B below).
One of the final goals of this project is to build a prototype of the next-generation electric city buses. The 10.7 meter long prototype bus will be charged in the depot overnight and should be able to cover a full day of regular operation (250-300 km) without additional charging opportunities, even in harsh winter conditions.
Electrified public transport carries the promise of many economic and environmental benefits but also imposes a number of technical challenges: The use of batteries in both small battery buses driving in local neighborhoods and larger trolleybuses for high-density urban areas raises new questions regarding the technical implementation of the charging infrastructure, its economic viability, and the operational stability of the entire vehicle fleet.
In an effort to address these challenges, the primary focus of the research conducted at IDSC is on optimizing battery size and charging strategy across the vehicle fleet of a public transportation network. In this sense, we move away from the concrete prototype vehicle mentioned above and follow a holistic optimization of the fleet that considers all currently available charging strategies, i.e., overnight depot charging, opportunity charging, and in-motion charging.
To this end, an open-source software tool is being developed that allows for answering a variety of related questions such as: what is the optimal battery size for each of the charging strategies?, how do the solutions for different strategies compare to each other?, what is the trade-off between battery aging and acquisition cost?, etc.
From a technical perspective, this work package involves benchmarking various optimization methods. In particular, analytical methods will be compared with generic ones and the advantages and disadvantages of the different methods will be investigated. The main objective of this benchmarking is the assessment of the potential of machine learning methods, especially when dealing with higher model complexity. As part of this research, our goal is to make use of a combination of different methods such as Non-Linear Programming (NLP), Dynamic Programming (DP), and Reinforcement Learning (RL) to take advantage of the intrinsic benefits of the different methods and get as close as possible to the global optimum.
Due to generally poor insulation and doors that open frequently, the energy required to achieve a comfortable environment for the passengers is generally high in city buses. In the case of electric buses, this issue is even more severe as, on the one hand, there is no abundant heat source such as a diesel engine and, on the other hand, energy used for the thermal systems cannot be used for propulsion. Obviously, both these peculiarities are intrinsic to battery electric vehicles and limit the achievable driving range. Furthermore, the auxiliary power consumption experienced in modern electric buses (which also includes other consumers, such as lights, computing hardware, and the infotainment system) can be even higher than the traction power consumption, see the figure below.

In external page previous research we were able to show that by incorporating a thermal reservoir in the form of a hot water cycle into the traction energy management, the lifetime of the traction energy management can be significantly increased. Building on these findings, one of the goals of the project is to identify and utilize the various thermal reservoirs in the Swiss eBus Plus prototype in a similar manner, ideally in both summer and winter operation. In principle, the high complexity of the thermal system allows for such a consideration but it poses new challenges. The vapor compressor cycle (VCC) can operate in both cooling (“air conditioning”) and heating (“heat pump”) mode. As a result, it can either provide heating or cooling to both the cabin and the traction system cooling circuit. Due to this cross-coupling, waste heat in the traction system can be utilized to heat the cabin. Using classical control theory, it is difficult to account for all the influences present in this system. Therefore, an optimized thermal management strategy is to be devised that is based on a physical model of the entire system.
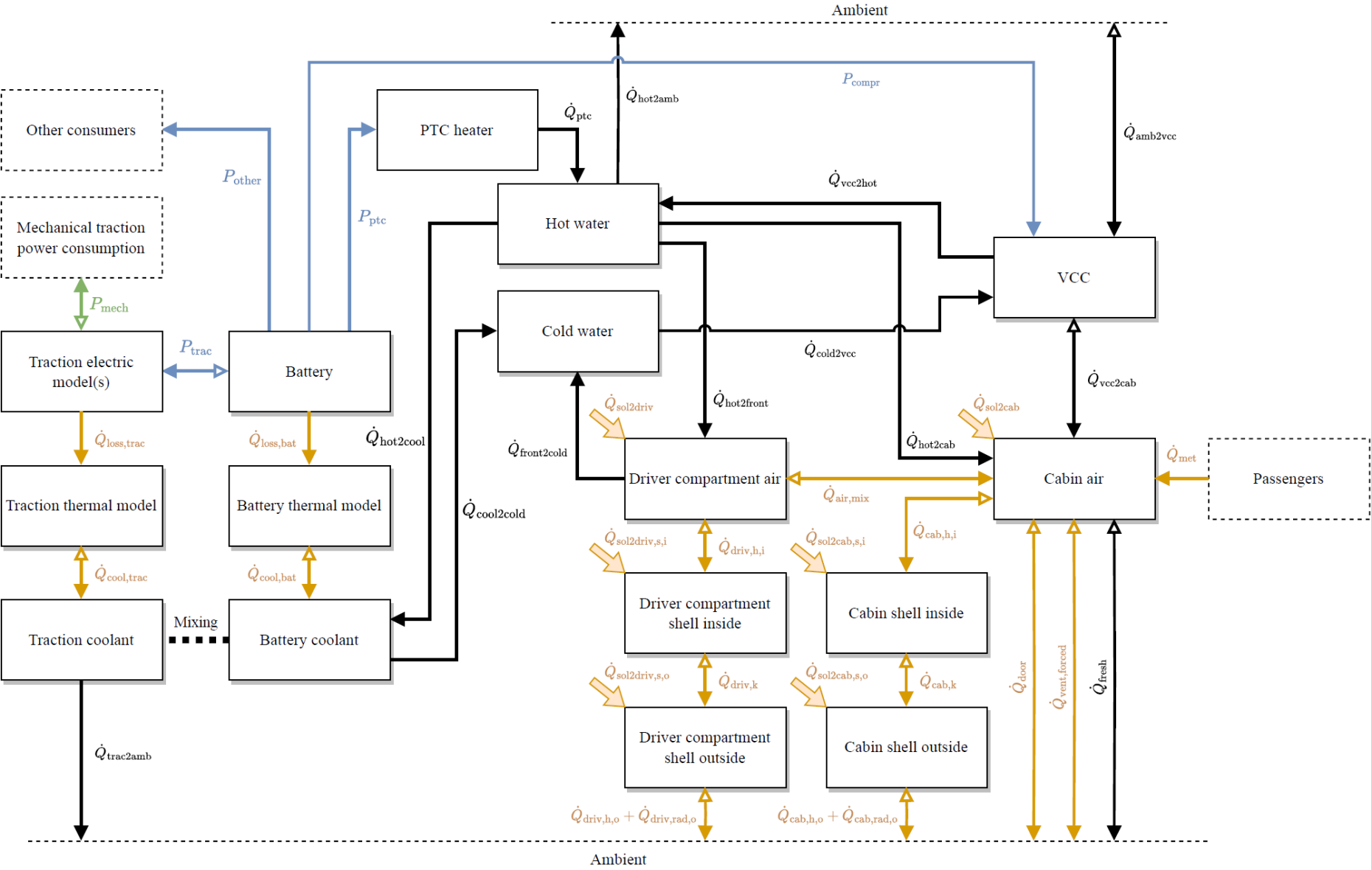
The system under consideration is subject to an inherent trade-off between the energy consumption of the thermal systems and the achieved thermal comfort. For instance, thermal system energy consumption can be reduced in winter by lowering the cabin temperature set point, which, of course, is at the expense of thermal comfort. This trade-off has been quantified in a external page previous publication based on steady-state thermal models. As a next step, an intelligent thermal management strategy is to be developed, which will provide a tuning parameter to vary this trade-off according to the needs of the end user, i.e., the public transport operator. For them, such variations are of great interest to determine the amount of energy (and thus money) to “invest” in thermal comfort.
The research performed in this field builds upon the knowledge gained in the preceding research project called ISOTHERM.
- Based on the data collected in the previous research projects SwissTrolley plus and ISOTHERM, we curated a publicly available dataset, which consists of more than a thousand missions throughout all seasons, each usually covering a full day of operation. We call this data collection the Zurich Transit Bus (ZTBus) dataset. An accompanying data descriptor paper is currently under review at the journal "Scientific Data". A preprint is available external page here. The dataset is hosted on the external page research collection.