ISOTHERM
Riding comfortably in busses that use little electricity
The Swiss Federal Office of Energy (SFOE) has published an article showcasing some of the findings of the ISOTHERM project. The article is aimed at a non-scientific readership and can be downloaded external page here.
This project carries out detailed investigations into the thermal systems of electrified public transit. Physical modeling brings insights into the optimal selection of components, as well as their optimal control. On this basis, an Intelligent Software for Thermal Energy Management (ISOTHERM) is developed for a prototype trolley bus.
Introduction
In electrified public transport, thermal systems can account for more than 50% of the vehicle's total energy demand. These systems include heating, ventilation and air conditioning (HVAC) of the passenger cabin, as well as thermal regulation of the traction components.
In HVAC, thermal comfort and energy consumption are inherently linked by a trade-off: In winter, for example, lower energy consumption can be easily achieved by lowering the target temperature in the passenger compartment. However, this is associated with a reduction in thermal comfort. The optimal thermal system should be "Pareto-efficient": With such a solution, an improvement in energy consumption or thermal comfort can only be achieved by compromising the other criterion.
Goals
- The developed mathematical models are used in simulations to develop an improved understanding of the system. Simulation studies are carried out to quantitatively assess the importance of various influencing and potentially competing parameters.
The same procedure is used to look for the optimal combination of components, including their respective sizing. Specific questions can be looked at in detail, such as for example the energetic influence of different insulation materials. - On the other hand, the mathematical models are used to improve the control strategy of the various components. In a central, integral thermal management system, setpoints are generated either for underlying controllers or directly for the components. In this way, the trade-off between energy demand and comfort is resolved pareto-optimally.
Apart from the presumed energy saving potential, model-based control offers options for simpler tuning, by introducing intuitive parameters and target values.
Based on the project objectives, four work packages (WPs) have been derived. The work packages are graphically represented in the figure above and explained in the following.
- Modeling: As a basis for the rest of the project, this first work package mathematically describes all thermal subsystems and the associated disturbances. The model is designed to be modular and extendable.
- Algorithm: In the second work package the basics for the optimization are laid. This includes the definition of cost function and constraints as well as the development of one or more suitable solution algorithms.
- Simulation: In simulation studies statements about the optimal design of the thermal systems in a city bus are made. This includes statements about technology combination and dimensioning as well as positioning of components.
- Online control: In the last work package, findings from the previous work packages are used to develop an integral control software for use on an electric city bus.
The characterization of all involved thermal subsystems in electric city buses and their interaction forms the basis for the work on the subsequent work packages. The overall system model is based on a modular framework, such that individual components can be easily exchanged, added or omitted. Machine learning alogrithms are used to identify model parameters from measurement data.
Data Acquisition
Data acquisition is particularly important in the modeling process. We plan to use the measurement data for the following two purposes.
- Parameter identification in gray-box models: These types of model descriptions are based on the underlying physics of the system. Parameters which are not known and are not easily measurable can then be identified comparing real-world measurements with simulation outputs.
- Model validation: The final versions of the models should be able to accurately predict the real system behavior. Sensor data will be used to check the validity of the model descriptions.
Modeling
The modeling process has been approached simultaneously from two different directions:
- On the one hand, physical modeling techniques have been applied to parts of the overall system. This modeling approach allows to gain insights into the hidden workings of the systems, where measurements are not available and hard to obtain.
- On the other hand, it was attempted to model the whole system as simple as possible, while still representing the key trade-offs.
It is only possible to make meaningful comparisons between different hardware combinations based on their respective optimal control. Otherwise a distortion of the results by a suboptimal control cannot be excluded.
The conflict between comfort and energy consumption must be resolved either by developing a suitable combined cost function or by defining additional constraints. In the course of this project, intuitively understandable parameters will be defined that reflect the different preferences of transport operators.
In order to do justice to the high-dimensional optimization space with many state and control variables, various solution strategies will be explored. Analytical methods will be used to better understand and simplify the mathematical structures of the problem. Numerical methods of different complexity will then be used to approximate the optimal solution.
As indicated in the work package breakdown, the goal is to achieve a complete separation of the optimization algorithm from the models to apply it to. Thus, the optimization tools need to be general-purpose.
In contrast to physical experiments, simulations can be useful to estimate the performance of different hardware combinations quickly and cost-effectively. Various strategies are either used individually or combined to carry out the high-dimensional parameter studies. Due to the large computational effort to be expected, simulations can be outsourced to a high-performance computing cluster (e.g. "EULER").
- For manually defined parts of the parameter space, a large grid search can be used to search for the optimal parameter combination. This strategy is not very computationally efficient, but has the advantage that it is easy to implement. In order to take account of the large solution space, the potential in various sub-areas should first be estimated in rough studies. Selectively, the most promising sub-areas can then be successively refined.
- Around a given solution, sensitivity studies with respect to certain parameters can provide valuable insights to determine favorable further research directions. We show such a study in a external page conference paper.
- In order to consider all dimensions equally, generic optimization algorithms could provide a remedy. For example, there are algorithms that use numerical methods to estimate the local gradient in order to strive for a (local) optimum. Stochastic approaches (e.g. evolutionary algorithms) try to localize minima by using a population of solution candidates.
- Finally, it would also be possible to include the component sizes as optimization variables in the existing optimization problem for optimal control. An example of this approach has been published in a external page research paper in the eTransportation journal.
Two advanced control approaches have been developed in this research project.
Intelligent Water Heater Control
The water heater on the bus consists of a simple resistive heating element. The standard hysteresis controller does not consider the state of the rest of the vehicle, most ntably the traction system. Rather, it turns on the heater to maximum power, whenever the water temperature drops below its lower bound. It stops heating when the water temperature rises above its upper bound.
A more intelligent control algorithm based on optimal control prefers heating the water when energy is available abundantly, i.e., during recuperating. On the other hand, if the power demand of the traction system is large, the heating system is temporarily disabled. Such an optimized heating strategy can reduce the amount of energy cycled throught the battery, thus reducing both losses as well as battery wear.
An intelligent adaptive water heating strategy has been developed for a battery-assisted trolley bus. It has been implemented and tested on a prototype bus of VBZ. Since around June 2022, the controller has been active for over 1000 h without any issues. Extensive data analysis suggests that it is effectively able to reduce battery degradation by about 12%.
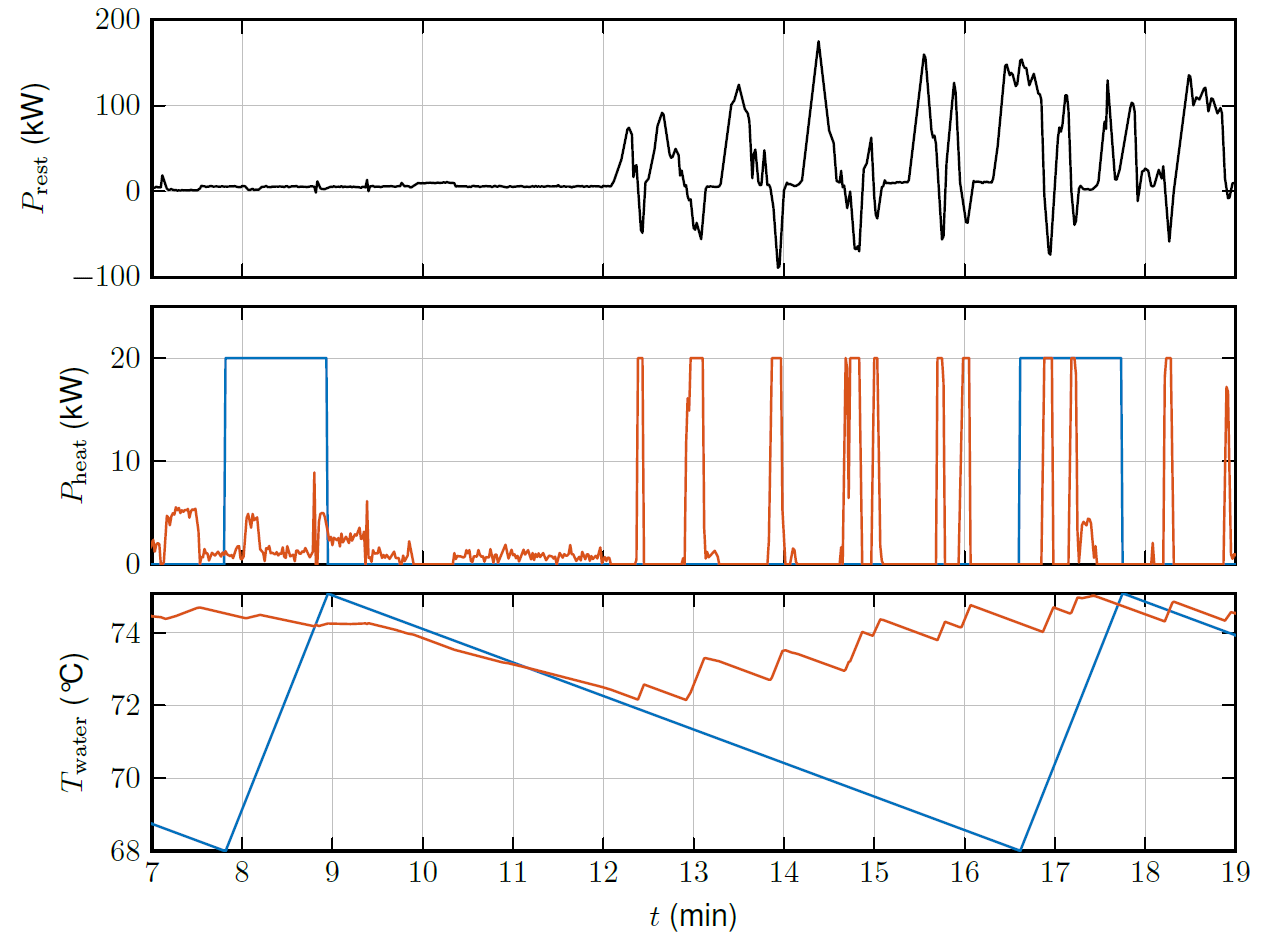
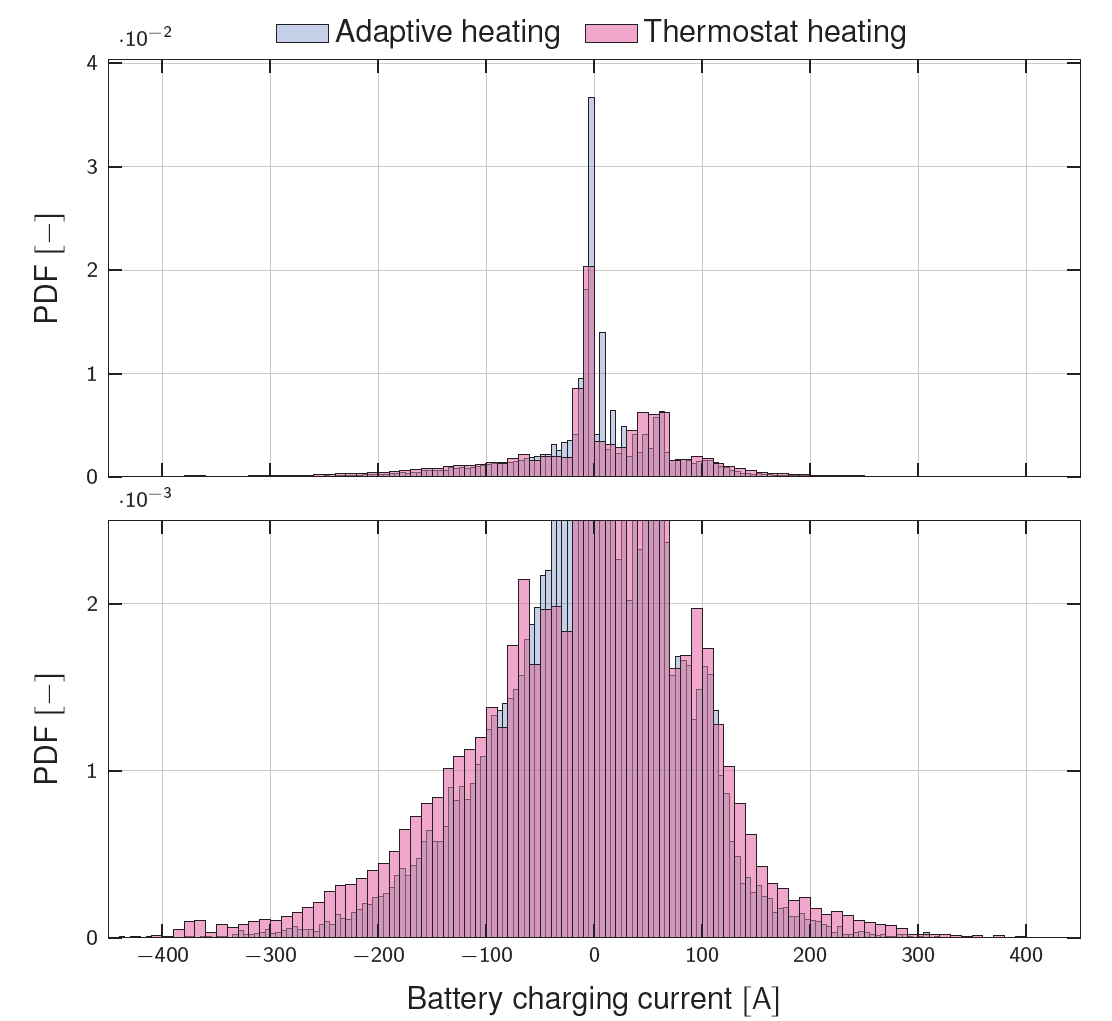
Closed-Loop Battery Health Target Tracking
To ensure that a battery can be operated for a certain period of time without using an overly conservative strategy or having to replace the battery prematurely, regular SOH measurements are required. Assuming that such measurements are available, for instance, once per year, a three-level control structure has been developed. In simulation studies, this controller is able to perfectly meet the battery lifetime requirements even in the presence of unmodeled disturbances.
The developed strategy is introduced in a external page journal publication.
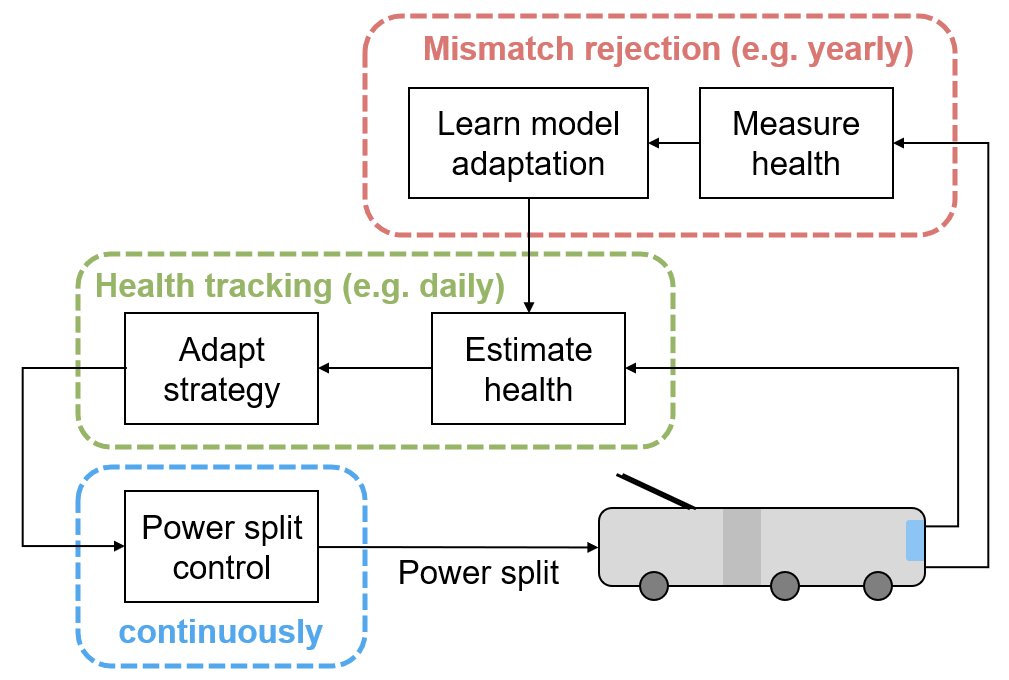