Thermoacoustic Oscillations: Modeling, Identification and Control
Diss. ETH No. 16550 by Andre Niederberger 2006.
Introduction
Modern premixed gas turbines for electricity generation have to comply with continually more stringent emission regulations, and therefore operate under lean conditions. This means that a lot of excess air is used to cool down the combustion temperature. However, this makes the combustor prone to thermoacoustic instabilities, blowout and flashbacks.

Combustion Instabilities are the most common form of thermoacoustic instabilities, where energy is transferred from a heat source to a fluid to cause oscillatory fluctuations. These oscillations lead to excessive vibrations, higher heat transfer to the walls and mechanical failures. In order to abate these oscillations, passive and active control approaches are proposed. Passive control is based on design changes or increased acoustic damping in the combustor through additions such as Helmholtz resonators. On the other hand, active control measures the state of the system and takes action accordingly. In our case, pressure fluctuations are measured and the fuel injection strategy is altered. This is promising because it can reduce the pressure oscillations and is able to cope with changing operating conditions.
In this multidisciplinary collaboration with our industrial partner ALSTOM, a test rig of a combustor has been set up in our lab, see Fig. 1. The air is electrically preheated and premixed with natural gas. The flame is stabilized by an EV burner, and the exhaust gases are subsequently discharged. Microphones distributed along the combustor measure the acoustic field. Loudspeakers as well as a secondary high-bandwidth fuel injector are used as actuators to decrease the pressure oscillations, which exceed 160 dB.
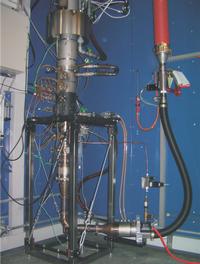
In order to design modern model-based controllers, a model of the combustor has to be developed. Our approach is based on a network model shown in Fig. 2. It consists of different blocks such as ducts, burner and flame. Each block is then described based on physical principles and also identified experimentally. The model is then assembled and various transfer functions can be extracted. For instance, the transfer function from a loudspeaker as actuator to a microphone pressure signal has been modeled and found to agree well with measurements, see Fig. 3.
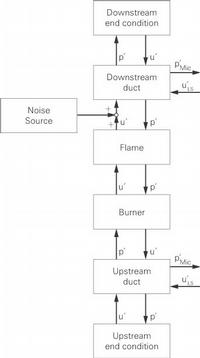
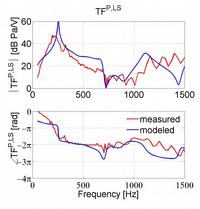
Passive control approaches using Helmholtz resonators have been evaluated, which can have a decisive effect in certain frequency ranges. However, changing this frequency range would involve hardware changes. Therefore, active control strategies are more promising. A robust H_infinity-controller has been designed with a loudspeaker as actuator, and found to be superior to a simple Gain-Delay algorithm.
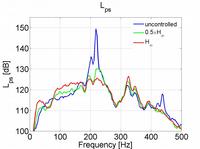
Moreover, a high-bandwidth fuel injector has been used to achieve more actuation power. It injects secondary fuel close to the flame to minimize transmission delays. A method has been developed which allows to find the transfer function despite high noise and saturation. This model has been exploited to design an H_infinity-controller, which performs best for various cases, see Fig. 4. In particular, the main peak at 218 Hz could be reduced by more than 25 dB. The identified model works well, see Fig. 5 for a comparison between the expected pressure reduction and the modeled one for an operating condition with three peaks in the frequency spectrum. Except for the low-frequency range, the model is very accurate. Model-based controllers give the designer the freedom to target selected frequency ranges, thus concentrating the control energy where it is desired.
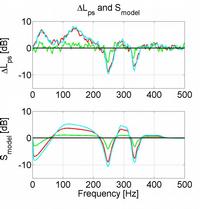
In addition, different controllers are improved online while the combustor is running, by using an evolutionary algorithm called CMA-ES. This allows to find an optimal controller in a changing environment. Figure 6 shows the cost function landscape for a Gain-Delay controller. The algorithm successfully finds the minimum value, and continues to track it despite changing combustor behavior, because of heat-up effect.
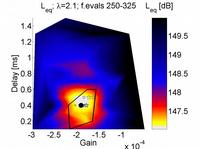
Niederberger, A. S. P., B. B. H. Schuermans, and L. Guzzella: Modeling and Active Control of Thermoacoustic Instabilities. In 16th IFAC World Congress, Prague, 2005.
Hansen, N., A. S. P. Niederberger, L. Guzzella, and P. Koumoutsakos: Evolutionary Optimization of Feedback Controllers for Thermoacoustic Instabilities. IEEE Transactions on Evolutionary Computing. Submitted for Review.
Niederberger, A. S. P., B. B. H. Schuermans, and L. Guzzella: Thermoacoustic Instability Modeling and Identification at Various Operating Conditions. ASME Journal of Measurement and Control. Submitted for Review.
Niederberger, A. S. P., D. Fritsche, K. Boulouchos, and L. Guzzella: Thermoacoustic Instability Suppression by Robust H_infinity Controller Design for Secondary Fuel Injection. IEEE Control Systems Technology. Submitted for Review.