Predictive Supervisory Control
Today's vehicle powertrains consist of various components, such as a conventional combustion engine, an exhaust aftertreatment system, and electric propulsion components, to name a few. The goal of the predictive supervisory control project is to develop a high-level powertrain coordinator that optimizes the interaction between these powertrain components and maximizes the powertrain performance.
Incorporating predictive information about the vehicle's mission allows us to optimize the powertrain operation specifically for the upcoming mission.
Using physical system models and online optimization, we aim to achieve transferability of the developed methods to various powertrain layouts. While the methodology is intended for various light-duty and heavy-duty vehicles, we consider a 3.5t delivery van as a use case in this project. To guarantee the transferability of the method, three exemplary powertrain layouts are considered.
Conventional powertrains feature a combustion engine and an exhaust aftertreatment system (ATS). In this layout, we consider a Diesel engine with a state-of-the-art ATS, featuring a particulate filter (PF) to trap soot and other particulate matter, and a selective catalytic reduction (SCR) system to reduce nitrogen oxides (NOx).
The engine operation is defined by two objectives, namely minimizing the CO2 emission and minimizing NOx formation. As these two objectives are conflicting, a trade-off needs to be found. Furthermore, the ATS can only reduce NOx if it exceeds a minimum catalyst temperature of around 200°C. This further affects the optimal operation of the engine, especially during a cold-start.
The objective of the supervisory controller in this powertrain layout is to limit NOx formation while heating up the ATS during phases where emissions are critical and minimize CO2 formation in phases where the ATS is working efficiently.
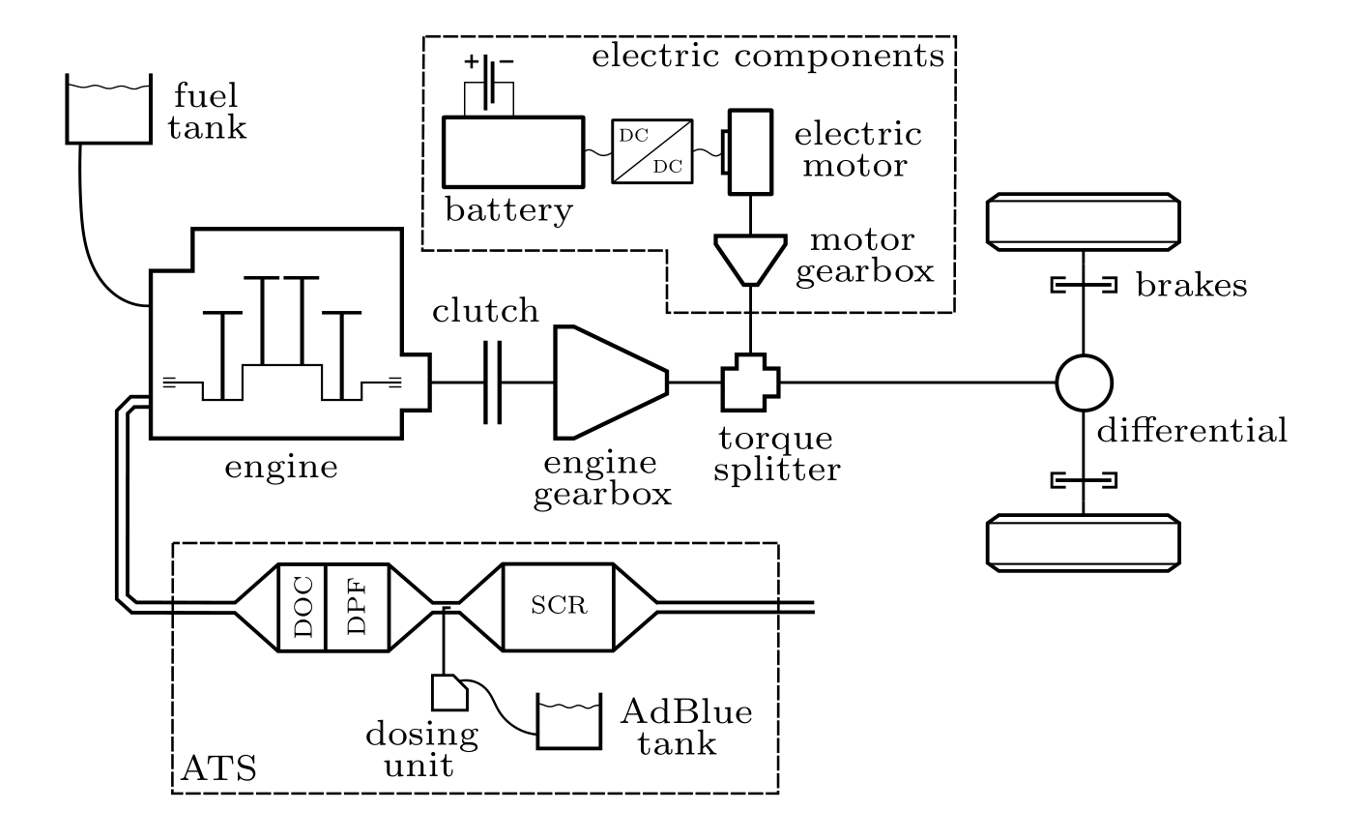
Through hybridization, a vehicle’s CO2 emission can be further reduced. In addition to the conventional combustion engine and the ATS, an electric propulsion motor and a battery are added to the powertrain. Besides these new components, the same vehicle and powertrain as in the previous layout are considered.
As the overall powertrain efficiency is increased, less energy remains to heat up the ATS. Furthermore, frequent operation in purely electric drive is likely to result in phases where the ATS temperature falls below its minimum operating temperature. This makes it even more important to carefully plan the vehicle's operation for the upcoming mission. Furthermore, the battery state of charge must be managed to allow sufficient boosting and recuperation capabilities throughout the driving mission.
When including the gear selection in the optimization, a mixed-integer optimal control problem results. As this type of problem is notoriously difficult to solve and the computational power onboard the vehicles is strongly limited, optimization methods tailored to the specific problem must be developed.
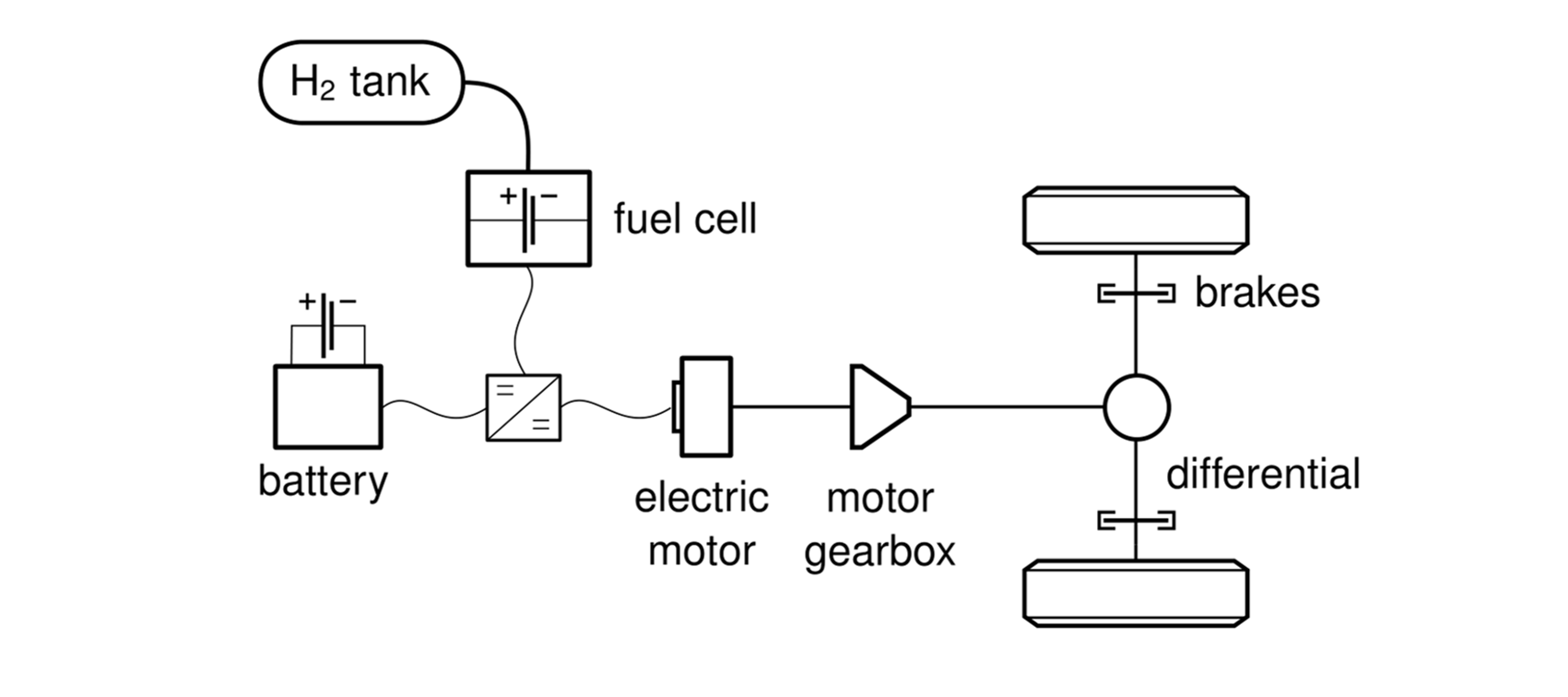
To validate the applicability of the developed methodology to future powertrain concepts, we consider a hybrid vehicle that features a fuel cell rather than a conventional combustion engine. As the fuel cell emits only water, an ATS is no longer required. However, the task of managing the battery's state of charge remains.
Johannes Ritzmann, Christian Peterhans, Oscar Chinellato, Manuel Gehlen, Christopher Onder, external page Model Predictive Supervisory Control for Integrated Emission Management of Diesel Engines, Energies, 2022
Johannes Ritzmann, Oscar Chinellato, Richard Hutter, Christopher Onder, external page Optimal Integrated Emission Management through Variable Engine Calibration, Energies, 2021
Johannes Ritzmann, Georg Lins, Christopher Onder, external page Optimization Method for the Energy and Emissions Management of a Hybrid Electric Vehicle with an Exhaust Aftertreatment System, IFAC-PapersOnLine, 2020
Johannes Ritzmann, Andreas Christon, Mauro Salazar, Christopher Onder, external page Fuel-optimal Power Split and Gear Selection Strategies for a Hybrid Electric Vehicle, SAE Technical Paper, 2019