Dynamic Emulation of a House in a Test Bench
The procedure for developing new control concepts for heat pump heating systems aiming at increasing the overall efficiency of the system usually consists of three major steps. In a first step the controller algorithm is developed in the simulation environment. It is then implemented in the controller hardware, which is tested in an HIL test environment (HIL: hardware in the loop). The task of the final step is to show that the new control concept truly is an improvement from the conventional control concept when it is applied in the real environment. The main disadvantage of the first two steps is the fact that the heat pump is only simulated. The final step involves a real heat pump, but the main problem of this step is the fact that two control concepts can only be investigated sequentially. Since the conditions are different, the comparison generally fails.
For the purpose of comparing different controllers sequentially at any period of time (not only during the heating period) and under identical conditions, a test bench for dynamical tests on a brine-to-water heat pump has been built at the Measurement and Control Laboratory. On this test bench it is possible to emulate dynamically, for a real heat pump, the thermal behavior of a house as well as the thermal behavior of an earth probe. Models of the thermal behavior of the house and of the earth probe are thus simulated in real-time. As a result, the reference temperatures for the inlet of the heat pump are calculated on the basis of the measured outlet temperatures of the heat pump and of selected weather data such as outdoor temperature and solar radiation. A control system ensures that these set points are tracked by the corresponding physical quantities at the test bench. Since these conditions are reproducible, the controllers can be compared among each other equitably under the same conditions.
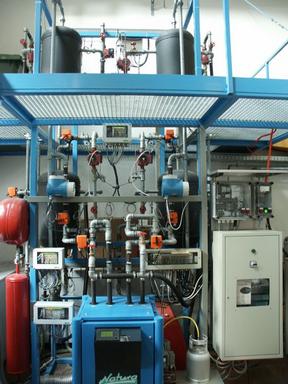