Aerial Construction
Building structures with flying machines
The Aerial Construction project is a collaboration between the Institute for Dynamic Systems and Control and the Chair of Architecture and Digital Fabrication. The objective is to investigate and develop methods and techniques for robotic aerial construction.
The project is carried out in the external page Flying Machine Arena.
Research
The pursuit is multidisciplinary, requiring the development of nonstandard material systems, advanced digital design and construction processes, and adaptive strategies for controlling the aerial robots as they interact with their environment and cooperate in the assembly task. Because the structures produced in this framework will be less constrained by conventional assembly parameters (such as, for example, the need of scaffolding to build from the ground upward), we expect that our work will foster new forms of architecture and construction methods [1].
The research carried out at the Institute for Dynamic Systems and Control focuses on:
- Physical human-quadrocopter interaction and contact with the environment
- Aerial assembly of tensile structures
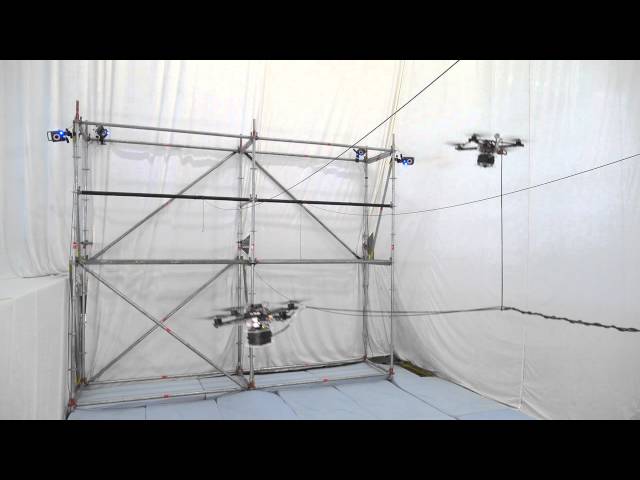
Building Tensile Structures with Flying Machines
Flying machines offer a number of advantages compared to traditional construction machines. Specifically, they can reach any point in space and fly in or around existing objects. However, they also have drawbacks, such as limited payload and accuracy. Tensile structures fit very well this combination of characteristics and constraints, and were subject of preliminary research in [2,3].
Eventually, a rope bridge that can support the crossing of a person was assembled by quadrocopters. The rope bridge acts as a demonstrator, showing for the first time that small flying machines are capable of autonomously realizing load-bearing structures at full-scale and proceeding a step further towards real-world scenarios. Except for the required anchor points at both ends of the structure, the bridge consists exclusively of tensile elements and its connections and links are entirely realized by flying machines. Spanning 7.4 m between two scaffolding structures, the bridge consists of nine rope segments for a total rope length of about 120 m and is composed of different elements, such as knots, links, and braid [4].
The vehicles are equipped with a motorized spool that allows them to control the tension acting on the rope during deployment. A plastic tube guides the rope to the release point located between two propellers. The external forces and torques exerted on the quadrocopter by the rope during deployment are estimated and taken into account to achieve compliant flight behavior [5]. The rope used for these experiments is made out of Dyneema, a material with a low weight-to-strength ratio and thus suitable for aerial construction.
Physical Human-Quadrocopter Interaction
Aerial construction requires UAVs to physically interact with their environment. To achieve this, one possibility are hybrid force-position control strategies. These are often used in assembly tasks with robotic manipulators, such as the peg-in-hole problem. Generally speaking, force control is used whenever compliance with the environment is necessary. Furthermore, force control enables physical human-quadrocopter interaction [5]. Physical human-robot interaction has been largely treated in the context of humanoid/mobile robots, however, physical interaction between a person and a UAV has seen little research activity. Reliable and safe physical interaction with UAVs will be of great importance in real world applications, where robots will tightly cooperate with humans, such as, for example, on a construction site [6]. We use a control strategy based on admittance control that can be used for both human-vehicle interaction and force tracking and makes use of a force estimator.
Publications
- [1] F. Augugliaro, S. Lupashin, M. Hamer, C. Male, M. Hehn, M.W. Mueller, J. Willmann, F. Gramazio, M. Kohler, and R. D’Andrea, “The Flight Assembled Architecture Installation: Cooperative construction with flying machines”, IEEE Control Systems Magazine, Volume 34, Issue 4, 2014, pp. 46 – 64
- [2] F. Augugliaro, A. Mirjan, F. Gramazio, M. Kohler, and R. D'Andrea, "Building tensile structures with flying machines", IEEE/RSJ International Conference on Intelligent Robots and Systems, 2013.
- [3] A. Mirjan, F. Gramazio, M. Kohler, F. Augugliaro, and R. D'Andrea, "Architectural fabrication of tensile structures with flying machines", in Green Design, Materials and Manufacturing Processes. CRC Press, 2013.
- [4] F. Augugliaro, E. Zarfati, A. Mirjan, and R. D’Andrea, “Knot-tying with flying machines for aerial construction”, IEEE/RSJ International Conference on Intelligent Robots and Systems, 2015, to appear
- [5] F. Augugliaro and R. D'Andrea, "Admittance control for physical human-quadrocopter interaction", European Control Conference, 2013, pp. 1805-1810.
- [6] J. Willmann, F. Augugliaro, T. Cadalbert, R. D'Andrea, F. Gramazio, and M. Kohler, "Aerial robotic construction: Towards a new field of architectural research", International Journal of Architectural Computing, Vol. 10-3, 2012, pp.439-460.
Previous work: Flight Assembled Architecture
Flight Assembled Architecture, a collaboration with architects Gramazio & Kohler, is an exploration in aerial construction. Conceived as a 1:100 model of a 600 m high vertical village, the four day long, live exhibition featured four quadrocopters building a 6-meter tall tower out of 1500 foam bricks. The exhibition took place at the FRAC Centre in Orléans, France from December 1 to 4, 2011. The FRAC Centre is an architectural art museum in the outskirts of Paris that promotes contemporary art, both nationally and internationally. During the opening night the museum hosted 300 enthusiastic people. Additional information about the project